The Devil is in the Detail
At Melett, we go to great lengths to ensure our parts are both engineered and manufactured to accurately replace or improve the original turbo design.
With precision engineering, you cannot simply see ‘quality’ and if you do not fully understand the detailed design requirements of a component, it is difficult to understand how these critical features impact the performance of the turbo.
To help you understand these features, here are some examples of the differences between a high quality product and its lower quality counterpart.
Accumulative Defects in a Core
Due to the operating conditions within a turbocharger, the level of precision in the manufacturing of turbo parts is extremely high and consistency is vital.
Why is this important?
It all comes down to accumulation of errors. Producing one component with 100% accuracy is a relatively simple process, to achieve the same level of accuracy when producing thousands of components is an extremely difficult task; without the use of strict manufacturing processes this would not be possible.
If one component in every hundred had a fault, it could be hugely detrimental when combining this with production figures and here is why.
Each core assembly contains up to fifteen components and if one in every hundred components is at fault, statistically there will be 15% of core assemblies produced with a component fault resulting in more warranties.
To produce quality on a large scale you need to use the correct materials, manufacturing processes and machinery combined with the correct quality systems – at Melett, this is what we do.
IHI RHF4/5 Thrust Bearings
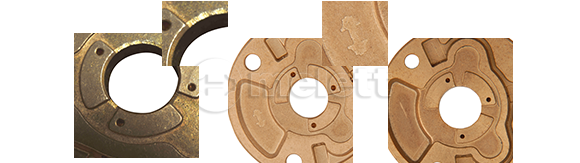
Lower Quality Sample (RHF4)
To the untrained eye, initial impressions are they look ok, however looking at the parts in more detail:
- The surface is very pitted – pitting can score the thrust parts and lead to premature failure;
- Badly de-burred;
- The edges are not clean and sharp;
- Often they have an over polished surface (focus is on aesthetics, rather than function);
- No controlled scratches to create surface tension.
Melett Sample (RHF4)
- Clean, sharp edges;
- Machined surface;
- No de-burring – when manufactured correctly this process is not a requirement;
- Performance mirrors the precision of the design;
- Controlled scratches to create surface tension.
When an engine is switched off overnight, if the surface is too smooth the oil will run off. The scratches create a surface to retain the oil and prevent run off, so when starting the engine in the morning there is already some oil present to lubricate the turbo.
OEM Sample (RHF55)
- Clean, sharp edges, similar to the Melett sample;
- Controlled scratches on the surface finish to retain oil.
What is Thrust Bearing Ramping?
There are a number of different ways to produce the initial thrust bearing blank, including cast bar, stamped strip, powder metal and hot forging. All thrust bearings then undergo various operations, including:
- Double disc grinding;
- Oil feed hole drilling, and most importantly;
- The ramp sizing on the oil pads.
Oil ramping is designed to allow the thrust bearing to resist the thrust forces put on it. It is essential to understand the importance of oil ramping and the part this plays in reducing wear and prolonging the turbos life. The ramp sizing is barely visible but is an extremely important feature on the thrust bearing. It creates a wedge of oil as the thrust component rotates and helps to force the parts away from the surface, reducing wear and therefore increasing the turbos life.
Oil Ramping Cross Section
RHF4/55 Bi-Metallic Thrust Washer
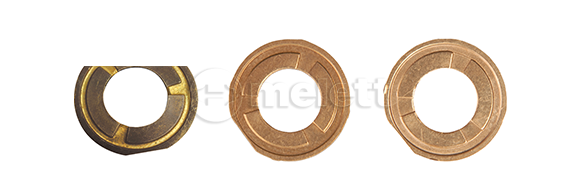
Lower Quality Sample (RHF4)
- No controlled scratches to create surface tension;
- Badly de-burred;
- Blackened colour;
- Pitted surface and edges – pitting can score the other thrust components and lead to premature failure;
- Doubts over the material quality?
Melett Sample (RHF4)
- Nice clean sharp bearing surface;
- Material is smooth, with controlled scratches on the surface;
- The surface is not scorched or pitted.
OEM Sample (RHF55)
- Clean, sharp edges, similar to the Melett sample;
- Controlled scratches on the surface.
Tooling – RHF4 Bi-Metallic Thrust Washer (1450-040-321) tool
Melett invests heavily in our own tooling to ensure each part is precision manufactured to the correct tolerances and specification.
- The tool for the RHF4 Bi-metallic thrust washer is a very intricate tool;
- Made in Japan, the multi-stage press tool – starts with a strip of bi-metallic material (copper and steel), which then goes through 9 different stages to create the finished product;
- Producing the correct tooling requires significant investment and usually cost tens of thousands of pounds.
When you purchase a low quality core assembly, unless you dismantle each core it is unlikely that you will know the quality of the parts contained in that core before installing it.
BV50 Thrust Bearing
Lower Quality Sample
- Blank has been cut from worn / low quality tooling;
- Thrust pads without clean and square edges. These thrust pads are rounded through excessive deburring – usually compensating for low quality tooling;
- Thrust ramping is too deep and uneven on each pad, and there is no apparent control over the ramp sizing – the most critical bearing feature; see Thrust Ramping;
- Surface finish is too smooth;
- Oil feed hole is too large.
Melett Sample
- Thrust pads – sharp square cut from quality tooling;
- Thrust bearing ramping size is controlled – correct size on all pads;
- Oil feed hole is clean, deburred and to the correct size;
- Controlled scratches on the bearing surface (as on GT15-25) to retain oil on shut down.
All Melett products are engineered using the strictest quality control processes. The team incorporates 3D measurement capabilities, down to a repeatable accuracy of 2 microns, along with traditional engineering measurement equipment and state of the art 3D modelling software to create the engineering drawings for manufacture.
GT/VNT 15-25 Seal Plate Screw
- The seal plate screw for the Garrett GT/VNT 15-25 turbo to the untrained eye looks like a normal screw you can buy from your local bolt supplier;
- These screws are fitted inboard of the seal plate O-ring;
- If a standard screw is used, it is possible for oil to work its way up the thread and leak into the compressor cover. To prevent this, the screw has a sharp feature under the head which digs into the seal plate creating the necessary oil seal;
- Melett accurate replacement screws are made on special tooling produced to ensure our parts contain this critical feature.
GT15 3 Part Thrust
When using the 1102-015-324 large pad thrust bearing, it is important that this is used in conjunction with the 1102-015-220 thrust spacer and the 1102-015-242 thrust washer, rather than the 1102-015-240 thrust collar.
Although these may appear dimensionally the same at first glance, this is not the case as the thrust washer and thrust spacer offer a different clearance to the thrust collar. If the thrust collar is used this can create premature failure of the bearing system.