Common Turbo Failures
Common turbo failure modes create much discussion between our customers and technical department. To help identify common failures in warranty situations and to provide advice on how to prevent future failures occurring, we have created a series of help guides:
Overspeeding
Overspeeding is a term used when a turbo is operating well above its normal operating limits.
So, what causes overspeeding?
- Engine modifications including ‘chipping’ or ‘over-fuelling’;
- Inconsistent flow of air into the turbo – this can be caused by a tear in the air hose or it becoming completely detached, or by restrictions in the air intake filter or pipe work;
- The wastegate or VNT mechanism has been set incorrectly;
- Worn injectors;
- Installing an incorrect turbo;
- Loss of signal to the SREA (Simple Rotary Electronic Actuator) for the wastegate or VNT control;
- Operation at altitude.
Visual effects of overspeeding
- The ‘orange peel’ effect;
- Inducer blade damage can be a consequence of housing rub;
- Staining due to oxidation;
- Partial loss of blades;
- Burst wheel.
The ‘orange peel’ effect explained:
‘Orange peel’ effect on the back face of the compressor wheel is created by expansion and contraction. When the compressor wheel overspeeds it grows in size. This expansion causes cracks between the grain boundaries of the material, in mild cases this returns back to its original state (like elastic) but in most cases these cracks begin to grow and eventually part of the hub can break away.
Quite often overspeeding is overlooked as a cause of the turbo failure as the symptoms of other failures can occur as a result of this overspeeding. Material transfer and discolouration of parts may indicate a lack of lubrication. Scoring to parts could indicate oil contamination, however the particles that have caused the scoring could have broken away from the bearings as a result of the overspeeding and imbalance caused by this.
This imbalance can also cause compressor rub and turbine wheel rub in the housings, which in turn can lead to the shaft snapping and loss to part of the inducer blades. All in all overspeeding causes a lot of damage and is often the primary failure mode! Recognising these features when diagnosing a warranty return can save time and money. For further information on this or other topics, please contact Melett Technical Support – [email protected].
Oil Contamination
Oil is very often overlooked as a critical component, however clean filtered engine oil is a major requirement and a necessity for all turbochargers. Contamination will cause rapid wear to various components and eventually cause catastrophic failure.
Signs of oil contamination:
- Scoring to thrust parts;
- Scoring to journal bearings;
- Scoring to journal bearing diameter of shaft and wheel;
- Smell of fuel in the oil.
Alternatively, if oil levels are too low or if the wrong grade of oil is used, the turbocharger will also fail. If the original cause of failure is not identified it is likely the same type of failure will occur on the remanufactured turbo. Catastrophic damage to the bearing systems can occur within seconds of the turbocharger commencing operation.
Common causes of oil contamination:
- High carbon build-up in engines quickly contaminates new oil;
- Contamination of new oil whilst servicing (accidental);
- If the oil filter is blocked/damaged or a poor quality oil filter is used;
- Degraded oil caused by excessive temperatures or extended service intervals;
- Engine wear and tear, leaving deposits in the oil;
- Fuel or water mixing with oil supply.
Turbo failure prevention:
- Using new oil and filters helps to reduce the risk. We advise that filters recommended by the engine manufacturer are used when refitting the turbo
- Replacement oil must be the correct grade for the engine
- Replacing or cleaning the oil inlet pipes and in-line micro filters helps to prevent carbon deposits or sludge restricting oil flow to the bearings.
For further information on this or other topics, please contact Melett Technical Support – [email protected].
Oil Leaks
Oil is very often overlooked as a critical component. Oil leaks can be caused by a variety of factors which often originate around the correct pressure within the compressor and turbine housing. When an oil leak occurs it is important not only to think of the piston ring as the seal, but consider the flinger/ bearing housing bore, piston rings as well as the pressure in the housings as a complete ‘seal assembly’ – these all work together to create a seal.
If any one part of the seal assembly is faulty it can have adverse effects on the other parts in the ‘seal assembly’. For example, a piston ring and flinger bore can be geometrically correct, but oil leaks still occur on the compressor side. This is because the third piece of the puzzle, the pressure, is not correct. If the original cause of failure is not identified it is likely the same type of failure will occur on the remanufactured turbo. Oil leaks can cause catastrophic damage to the bearing systems and occur within seconds of the turbocharger commencing operation. To help you identify and prevent oil leaks from reoccurring when carrying out a repair, the following highlights some of the main causes and the signs of oil leaks.
Causes of oil leaks to the compressor outlet:
- Blockages or restrictions to the air intake pipe, hose or filter can create a vacuum, causing oil to leak into the compressor housing;
- Air leaks in the intake hoses or at the intercooler.
Causes of oil leaks to the turbine outlet:
- Leaks within the exhaust system;
- A clogged bearing housing;
- Leaks in the EGR (exhaust gas recirculation) system.
Causes of oil leaks at both the compressor and turbine outlets:
- Restricted or blocked oil drain pipe from the turbocharger to the engine;
- Restriction, or clogging, of the crankcase ventilation system;
- Repeated hot engine shutdowns leading to carbon deposits (coke) in the centre housing;
- Physical damage to the turbo’s rotating parts and excessive bearing clearance (possibly caused by other failure modes);
- Excessive crank case pressure (blow-by from worn piston rings/bores);
- Fitting the incorrect turbocharger.
Preventing future oil leaks:
- Ensure air and oil drain systems are clear from blockages or restrictions;
- Check the exhaust system to make sure there are no leaks present;
- Ensure DPF (diesel particulate filter) and Catalytic converter is free of blockages.
Please note:
Oil leaks can occur on VSR (high speed) balancing machines as the ambient pressures required to create the seal are not present as no housings are used. This can then force out oil from both the compressor end and turbine end giving the impression of a leak. This is unlikely to occur when the replacement turbo is fitted to the engine. An oil leak can also occur when engines are running on idle. The pressure within the housings is lower, which in turn can lead to a vacuum being created, causing the oil to leak into the turbine housing. Once the engine starts to run at normal speeds the pressures will be restored and the leaks will stop. For further information on this or other topics, please contact Melett Technical Support – [email protected].
Lack of lubrication / Oil Starvation
Below we have highlighted the causes and the signs of oil starvation, to help you identify and prevent oil starvation from reoccurring when carrying out a repair. If the original cause of failure is not identified it is likely the same type of failure will occur on the remanufactured turbo. A lack of lubrication can result in catastrophic damage to the bearing systems which can occur within seconds of the turbocharger commencing operation. Quite simply:
- If oil levels are too low, the turbocharger will fail;
- If the wrong grade of oil is used, the turbocharger will fail;
- If oil becomes contaminated, the turbocharger will fail.
Signs of lack of lubrication / oil starvation:
- Material transfer (caused by high temperature due to friction from bearings) to other thrust parts and the journal bearing diameter of the shaft and wheel;
- Discolouration to the thrust parts and the journal bearing diameter of the shaft and wheel;
- Excessive wear to the thrust pads of the thrust bearing;
- Excessive wear to the journal bearings.
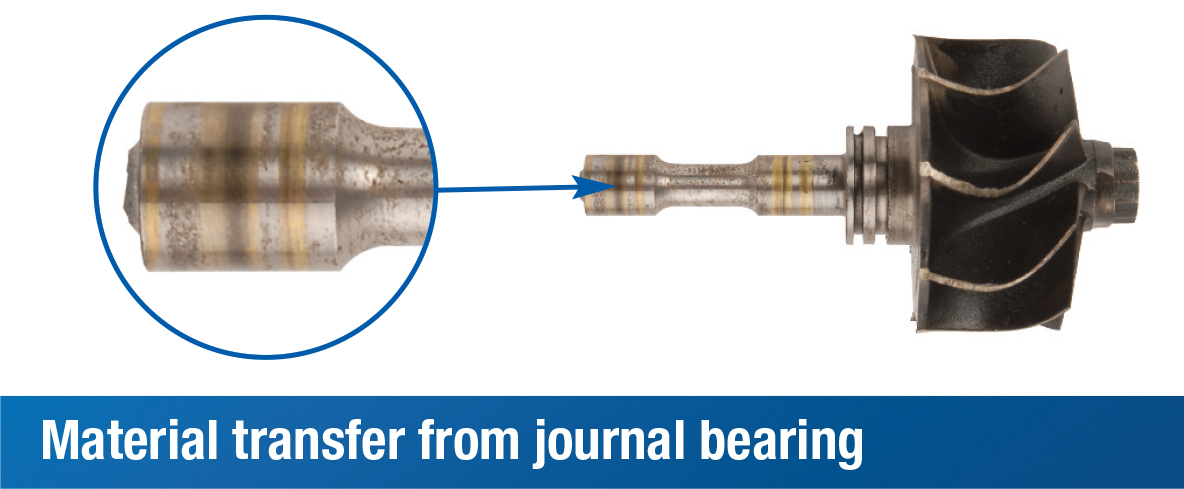
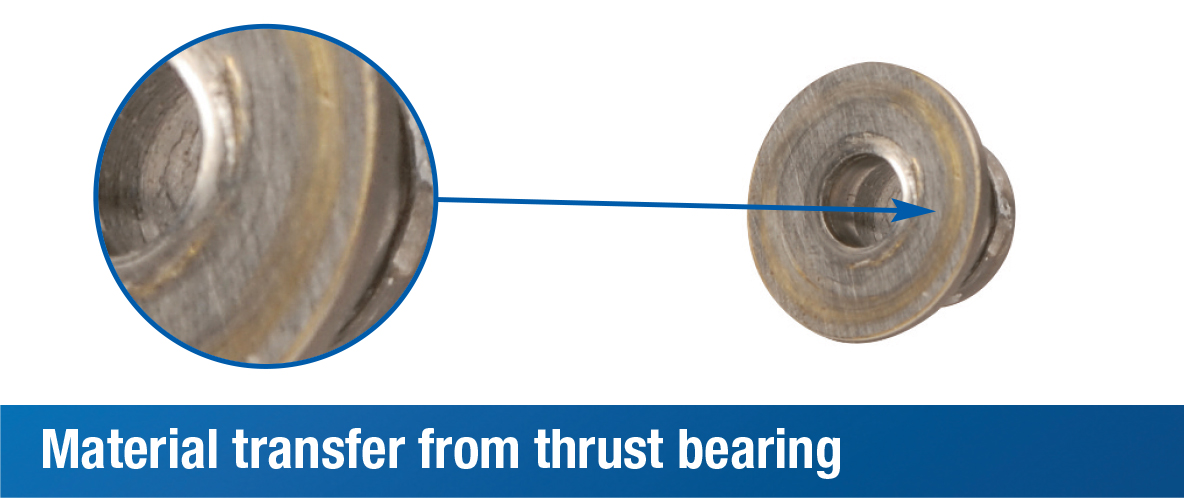
Causes of lack of lubrication / oil starvation:
- Poor oil filter maintenance;
- Insufficient oil in the sump;
- Incorrect oil inlet gasket used leading to restriction in oil supply;
- Build-up (coking) / carbon deposits in the oil feed pipe;
- Applying silicone to the oil inlet gasket causing blockages;
- Sludge or coke build up in bearing housing from hot shutdowns;
- A damaged, blocked or low quality oil filter;
- Failure to prime the turbo with oil before initial run;
- Engine left idle for long periods, especially during cold weather;
- Oil feed pipes containing bends or kinks;
- Engine wear.
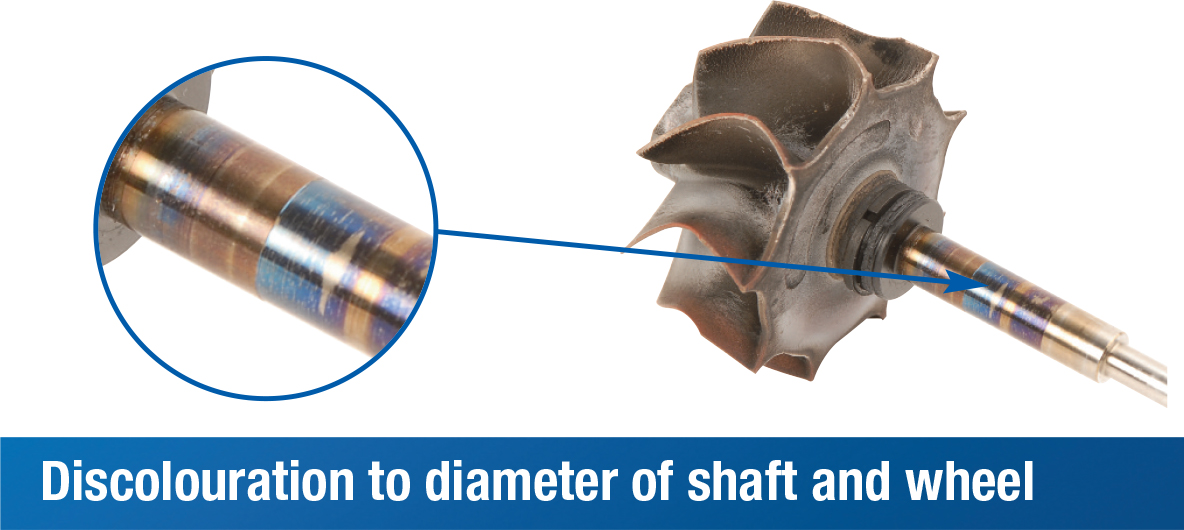
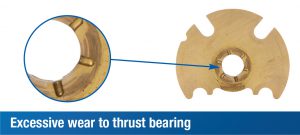
Preventing turbo failure caused by lack of lubrication / oil starvation:
- Oil supply to the turbo is critical, always check oil pressures are correct;
- Avoid using silicone on oil gaskets as they can easily become detached and block oil passages;
- Clean or replace oil inlet pipes to remove carbon deposits or sludge that could restrict oil flow to the bearing systems;
- Use fresh oil and new oil filters (which have been recommended by the engine manufacturer) when fitting a replacement turbocharger.
For further information on this or other topics, please contact Melett Technical Support – [email protected].
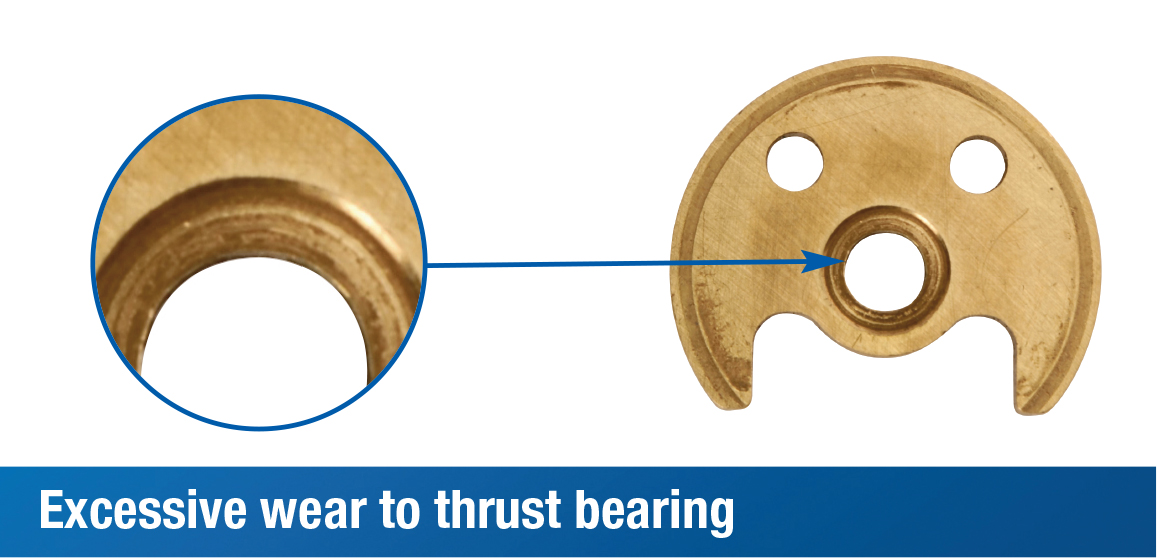
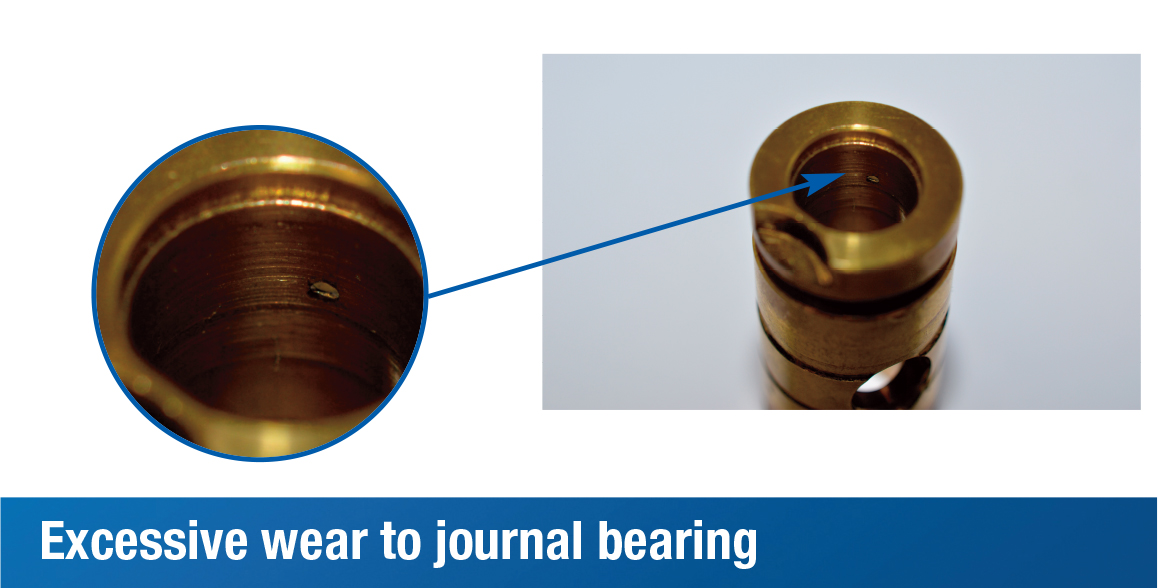
Foreign Object Damage
What is a foreign object and what causes it?
A foreign object is simply any object that enters the turbocharger through the air inlet or exhaust inlet. When a foreign object enters the turbocharger, its performance will be affected very quickly.
Signs of foreign object damage:
- Noise from the turbo during operation;
- Loss of performance;
- Chipping of compressor or turbine blades;
- Pitting around the compressor inlet;
- Pitting on the compressor blades.
Causes of foreign object damage:
- Small particles entering through damaged hoses;
- If the air filter is damaged (or faulty), of a low quality or missing, objects will be sucked into the air intake;
- Debris from a previous turbocharger failure;
- Broken engine components, e.g. valves or fragments of damaged piston, injector tips;
- Bolts, nuts, washers, rags or other items left in the intake pipe during servicing.
Preventing turbo failure caused by a foreign object:
- Make sure air hoses are clear from blockages and other loose objects;
- Check that air hoses are intact and in good working condition;
- Ensure the air filter is the correct one for the vehicle;
- Ensure no debris or engine fragments remain from the previous turbo failure;
- Using new gaskets helps to prevent the possibility of gasket break up and also ensure a perfect seal.
Please note: Never continue to operate a turbocharger with damaged blades as the rotor balance will be affected and this could impact its service life. For further information on this or other topics, please contact Melett Technical Support – [email protected].
REA/SREA
REA/SREA Failure Modes
REA (Rotary Electronic Actuator) or SREA (Simple Rotary Electronic Actuator) are fitted to many variable geometry turbos and control the variable vane movement. This article explores the benefits of the REA and possible causes or symptoms of failure.
What is variable geometry and why are these systems used?
When a turbocharger is matched to an engine, it is essential to balance the low speed response with high speed efficiency. The nozzle ring assembly is designed to change the exhaust gas inlet area with the engine speed to closely match the desired boost requirements of the engine. As the engine speed increases, the electronic actuator moves the nozzle ring assembly vanes to the fully open position to maximize the exhaust gas flow.
REA / SREA electronic actuators are highly complex and intricate. They are not interchangeable with different gearboxes or black caps. The calibration settings are programmed in the software within the black cap and are unique to each turbocharger.
Benefits of Electronic Actuators Include:
- Rapid response to changes in speed;
- Accuracy of minimum and maximum air flow;
- Feedback loop to the vehicle’s ECU – indicates where the actuator position is and learns what boost is required.
Faulty Electronic Actuator Symptoms:
- Complete loss of power, causing the vehicle to go into limp home mode;
- Flashing engine management light;
- Intermittent low pressure, or over boost.
Common Failure Modes:
Gearbox Failure – REA and SREA will fail as a result of the variable geometry mechanism sticking due to sludging or carbon build up. When the variable geometry mechanism sticks, it pulls a higher current through the motor than it is designed to take, this therefore causes the motor to burnout or the plastic worm gears to fail. This restriction can reduce boost pressure and can result in the vehicle being put into ‘limp home mode’. In most failures, the black cap and electronics are unaffected by the gearbox failure and can be reused.
Board Connectors – The wire connectors can expand and contract, eventually breaking and causing failure of the electronic actuator. This fault can often go undetected during repair and workshop testing, as the fault can only be detected once the actuator heats up.
Mishandling of the Turbo – If the turbo connector is knocked or banged, it will break and the whole unit will need replacing.
Water Ingress – The location of a turbo in the engine compartment can mean the electronic actuator is more susceptible to water ingress. The actuator can become rusty and contaminated, giving the wrong signals and ultimately breaking.
Engine Vibration – Constant vibration from the vehicle can wear the electronic actuator out, causing it to fail over a period of time.
Loss of Power – If the electronic actuator has failed to open the nozzle ring assembly vanes under acceleration, the turbo will fail to operate efficiently. If the vanes are set to a closed position, it can cause choking of the engine or overspeeding of the turbine. Alternatively, if the vanes are open more than is required, the turbo will have too much ‘lag’ and be slow to respond. If this occurs, it is essential to check if the electronic actuator has failed as a consequence of other failure modes.
Notes for Repair:
- When repairing the electronic actuator the worm gear and motor must be the correct ratio to avoid immediate failure.
- REA actuators must be calibrated to the turbo after repair. Incorrect calibration of the electronic actuator when assembled on the turbocharger can result in poor performance.
- Soldering to repair broken connections in the gearbox and black cap is not advised. Solder is susceptible to cracking in environments with temperature variance and vibration. For this reason, the motor and motor choke assembly connector must be spot welded.
For further information on this or other topics, please contact Melett Technical Support – [email protected].